Ink circulation systems have become de rigueur in the apparel and textile printing industry due to the increased use of direct-to-garment (DTG) and direct-to-film (DTF) printers.
DTG and DTF printers use water-based pigment inks, which “are fantastic because they can be used direct-to-garment and adhere to fabrics really well,” said Marc Vila, director of marketing at ColDesi Inc. They also can be used to print on natural fiber textiles as well as polyester-based fabrics.
The presses use white ink as a base coat so that printers can produce full-color prints on dark-colored fabrics. “This is where you are going to start running into circulation systems just because of the nature of that ink and how the ink is created,” he said.
White ink acts differently than CMYK colors in that it is made from titanium dioxide, which will settle to the bottom of the machine if it sits too long. Most new DTG and DTF printing presses come with ink circulation systems already built in to keep the ink from separating, which can clog the lines or printheads. Water-based CMYK inks don’t need to be recirculated to run smoothly through a printer.
White ink, in particular, needs to be maintained through agitation even before it is placed into the machine, either through shaking, stirring, or rolling the bottle, depending on the technology of the inks being used.
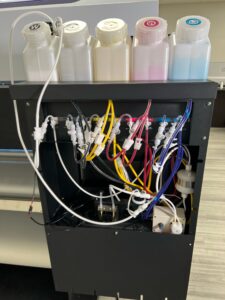
Vila calls white and metallic inks the highest maintenance inks because there is something inside the liquid to make them turn white, gold, or silver, which is a more complicated process than making a liquid turn magenta, yellow, or cyan.
“Agitating those inks is even more important because the materials inside those inks are more likely to settle and make the ink unusable or cause trouble in machine maintenance,” he said.
It is important to remember that every printer model and every ink type reacts differently, so maintenance will vary. Just because one solvent printer doesn’t require maintenance doesn’t mean another won’t or that every white ink printer will be hard to maintain, Vila emphasized.
Terry Combs, a well-known screen-printing expert who also works in sales and training at Franklin Lakes, New Jersey-based Equipment Zone, said that “some machines on the market are repurposed paper printers. You have to turn them on every day to get stirred up.” Most shops will take their white ink cartridge out of the printer in the morning to shake up the ink before putting the cartridge back into the machine.
The moment white ink is loaded into the printer, some of it will be pulled into the recirculation system. That means there is always some ink in the system that needs to be agitated frequently while it is on. It really depends on the machine how long a shop can leave a printer turned off before there is an ink clogging issue.
“If it does clog, sometimes you can get it unclogged by soaking the printhead in distilled water, or there are other chemicals people will use. You reach a point, if it doesn’t unclog, where you have to replace the printhead, which can get very expensive,” Combs said. Printheads run from $750 to $2,500 per printhead.
It is important that shops follow instructions from the manufacturer. Many of them will spell out how often a printer needs to be run before there is a clogging problem.
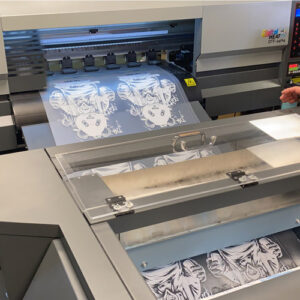
DTG presses print best on 100% cotton or high-cotton blends. DTF printers are also water-based, but because the ink is being placed on transfer film first, the designs can be placed on virtually any fabric, he said, which is “the big benefit.”
Estevan Romero, brand marketing lead for All American Print Supply Co. in California, said “we have never seen an impact to our industry in the way we are seeing with direct-to-film. Water-based DTF printing has disrupted every corner of the apparel/textile world with its unlimited color range, cost-efficient production process, and near endless material compatibility.”
He also believes that water-based inks are the best option for apparel and textile printing.
“Unlike other types of ink, water-based does not contain plastic, so production is far more eco-friendly,” he said. “As far as feel, water-based ink is much softer to wear and offers higher flexibility and comfort — even in large coverage areas. This type of ink is also ideal for fine details/sharp edges and is proven to last longer in the washer/dryer.”
Romero added that he believes DTF is “by far becoming the most popular and accessible means to begin high-end apparel printing regardless of budget or production volume.” That’s because most printers, from desktop setups to industrial roll-to-roll operations, can print on transfer film.
ColDesi’s Vila said that every printer his company sells or produces has different maintenance instructions when it comes to ink.
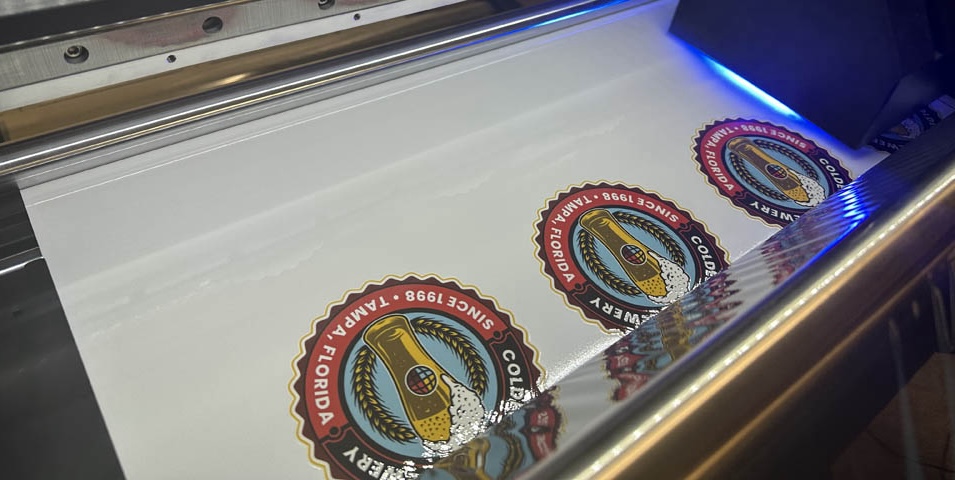
“An important lesson is don’t assume you know, even if you have experience, and make sure to communicate with the manufacturer or distributor very clearly on the type of ink you have and how to maintain it on the shelf and in the printer,” he said.
Another factor that can cause issues with the ink is if the printer is in an environment with extreme temperatures or humidity.
“If the press is kept in a low-humidity environment, the water or liquid in the ink will take the opportunity to escape into the environment and balance things out. If it is in a high-humidity environment, that is less likely to happen. It will help with the life of the circulation system, the life of the printhead, and the life of the ink on the shelf. All things that are really important,” Vila added.
Best ink for the job
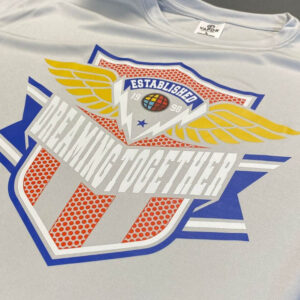
Dye-sublimation, which is a popular apparel decoration tool, prints ink onto special transfer paper. The ink is then heated up with a heat press, and the press turns the ink from a solid to a gas, infusing the ink into the fabric. The process gives the garments a softer feel than those printed with screen printing and other processes that lay ink on top of the fabric. Because the ink infuses into the garment, the process works best on white or lighter-colored fabrics.
If a shop is primarily printing on polyester for sports team jerseys or workout apparel, dye-sublimation is the best option because of the soft hand, efficiency, vibrant colors, and color fastness, said Rob Almstrom, CEO of American Print Consultants in Pennsylvania.
DTG printers work well with natural fibers, essentially the same type of materials that are used in screen printing. Most garments will need to be pretreated before printing so the fibers will accept the ink.
In DTF printing, a mirror image is printed on the film with a layer of white ink over the top of it. The film then receives a coating of adhesive that sticks to the white ink when it is still wet before going through a curing oven. The heat melts the adhesive onto the surface of the print. The print is then flipped over and placed on the garment where it is pressed with a heat press, Romero said.
Ink and recirculation technology have improved over time, “allowing that market to grow,” he said. “Textile pigment will continue to take more production away from screen printing and dye-sublimation.”
He added that the industry will see less and less of acid-dye printing because DTG and DTF are revolutionizing natural fiber printing. And even though acid-dye printing produces a high-quality product, it is time-intensive and requires a lot of water.
For textile pigment inks, the “increase in the quality of the inks and the introduction of circulation allows it to be a real player in the textile decoration game,” Romero said. “Without that, it stalled from the crash in 2009. It disappeared and dye-sublimation took over. Now it is finally coming back. The cost of inks and the cost of materials and equipment is relatively similar.”