Laminators are some of the workhorses of the print and graphics industry, lasting years without any problems, but that doesn’t mean print shops shouldn’t take a peek at the latest lamination technology. New innovations in both laminates and equipment can help new and existing shops increase their capacity, save time, and improve product quality.
There are two types of laminate: film, which is applied with cold or heat; and liquid laminate, which dries instantly when cured with UV light.
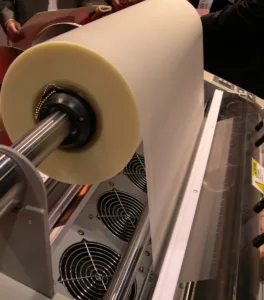
“Today, both film and liquid lamination are used for UV protection, image enhancement, and total durability,” says Carl Hoffman, dealer manager for Graphic Finishing Partners in Maryland Heights, Missouri. “Film lamination provides a thicker protective surface coating over liquid lamination, but both are used in today’s signage market. Film lamination most times needs to be applied with a laminator but can be hand applied, whereas liquid lamination can be brushed or rolled on, sprayed, or applied with an automated liquid coater.”
Liquid lamination has an advantage over film when applied to surfaces such as canvas, textured wall covering, or banners that do not have a smooth surface, as the liquid will conform to the high and low areas of the material,” he adds.
Another benefit of liquid lamination is that it can be applied to wall graphics after they have been installed, while film laminates need to be applied to the graphics beforehand.
Film has been a popular option for years, but liquid lamination is starting to come into its own in the sign and digital graphics market as commercial printers find new and innovative ways to use today’s more advanced materials, including for wall coverings, says Syd Northup, Marabu’s VP of digital inks and coatings for North America.
Companies wanting to change the texture of their signage should use film. Those that want UV or graffiti protection can use either type of laminate.
Marabu has been involved with the liquid lamination market since it acquired Clearstar Coatings in 2007. Before arriving at Marabu and taking over as VP of digital inks and coatings, Northup ran his own print shop, so he has worked with both types of laminators. What he has found is that not all print applications work well with film or liquid laminate.
Liquid works better for wall coverings than film because it doesn’t have a sheen to it, he says. “It’s not really going to protect it like a liquid laminate would, so it comes down to application.”
One reason sign and graphics shops consider shifting to liquid laminate is that films have become more expensive.
Liquid laminate ranges from 8 cents per square foot on the low end to 20 cents per square foot on the high end, depending on the volume and what products are being laminated. Films can cost $1-2 per square foot or more.
Marabu’s Star Lam Liquid Laminator is an inline coater for water-based-only products. The company offers a 64-inch machine or can manufacture 8-foot and 10-foot-wide machines. The ClearShield Select formulations come in gloss, semi-gloss, and matte finishes for manual and automated applications and work well on a wide range of printed graphics, including vinyl, banners, and rigid substrates.
ClearShield Select for StarLam is formulated for use with roll-to-roll liquid laminators, like the StarLam 1600R, on digitally printed vinyl, banners, and fleet graphics.
“The material is rolled in and passed through the metering bar, which is important. That way it spreads a consistent amount of liquid laminate onto the canvas or onto the wall graphic with texture on it,” Northup says. The machines are set up for a single operator. Once the roll of material is set up it passes through an infrared dryer.
“From unwind to rewind, a roll of media can take an hour and a half and a gallon of our product to coat an entire 150-foot roll. You are not dealing with the weight of film and the cost of film,” he says. “That has been a big reason people are looking at this now.”
Liquid laminate is perfect for outdoor signage and wall graphics that are in non-high-traffic areas.
Marabu works with a number of customers that use liquid lamination to coat art on cruise ships or indoor signage for amusement parks, arenas, and coliseums.
Another area in which liquid laminate shines is when a print involves texture of any kind. Film laminate would obscure some of that texture, but liquid laminate moves into the contours of it.
The company’s most popular liquid laminate, ClearShield, is a water-based product. Many smaller print shops hand-apply liquid laminate on the signage they produce, but once they get enough of that type of work, it makes sense to move up to a Star Lam laminator, which allows shops to buy liquid laminate in bulk and save money.
The pandemic did have an effect on the liquid lamination market due to raw materials shortages, but Marabu produces everything in Charleston, South Carolina, “so we were able to control our ability to make or create new products,” Northup says. “I don’t know if we really had a major increase versus film. I never looked at the variance, but we maintained our business through COVID. We got through it.”
Film laminators
Film laminators are a different animal than liquid laminators, says Sol Gnatowsky, Royal Sovereign’s Western regional sales manager/graphics, who has worked in the graphic and lamination market for more than 37 years and has had a hand in designing lamination equipment. He says that there are three factors involved in successful lamination using films: time, temperature, and tension, and newer technologies can help improve all three for better results.
Time is the speed at which the laminator operates and is critical to the output of any job, he says. If the machine runs too slowly, it “can cause wrinkles, and too fast can cause silvering in the back areas of the print.”
Royal Sovereign’s factories have developed a specialized frequency controller that allows precise and accurate stability of the speed controller. “Many different lamination films and media depend on repeatable time for repeatable results from job to job,” Gnatowsky says.
The advent of new temperature controllers gives shops the ability to vary the temperatures of the rollers, whether it is for warm roller settings, such as in the Sigmont 55H, Sigmont 65H, and RSC 6500H; or for hot lamination with the company’s Thermal 45” RSH 1151 or 65” RSH 1651 laminators.
“All have thermal sensors that assure exact repeatability of the temperature settings, and all have thermal cutouts that prevent any damage to the rollers of the laminators for excessive heating,” Gnatowsky adds.
As for tension, he says that “exact and proper tension is never automatic. This is where operator experience comes in. As you place a new roll of lamination film on the mandrel you will have heavy tension on the machine. As the film gets used, the roll gets lighter in weight and tension must be applied to the top and bottom mandrels manually. This is achieved by turning the tensioning mandrels on the side of the spindle. This will prevent wrinkling and boat waking of the films.”
The composition of the rollers is also very important as they put a force of 30-50 PSI on the film and media, he adds. Royal Sovereign uses crowned rollers to prevent them from flexing on the lamination media and boards, which could cause air pockets and wrinkling when running long prints—such as those used in the ad wrap world.
Graphic Finishing Partners recently launched a 63-inch heat assist laminator with added features that simplify the steps required for operating a laminator, Hoffman says. The laminator comes with a 10-inch tablet-style interface that controls all functions of the laminator, including the home screen, roller gap, pressure, brake tension, direction, and heat assist temperature. The device is supported by an integrated Roll Label Printer.
“Within the functions of the digital control panel, you can enter such things as the brand of laminate, surface type, and set the length of the lamination roll,” Hoffman says. “As you run production, the laminator will count down the length of laminate used, and at the end of the job, you can print out a label to identify the roll of laminate, including the remaining length of the roll. This is a wonderful feature not seen with most laminators.”
The LCD color display also offers an onboard operator help tutorial to assist users with any operational questions, and two inline rotary slitters give the option to slit the laminated material as it exits the machine.
“This feature is great for trimming the output edges during production or slitting the material into individual sections in order to support postproduction. All of these standard features improve repeatability, time, and efficiency,” Hoffman adds.
Film laminate will give added rigidity to prints when needed, and film is the preferred laminate for vehicle graphic installation because of the added thickness, which makes applying graphics to a vehicle easier in most cases, he says.
Most film laminates are waterproof, while liquid laminates are only water-resistant, Hoffman says, “so, if moisture is concerned, film would be the better choice.”