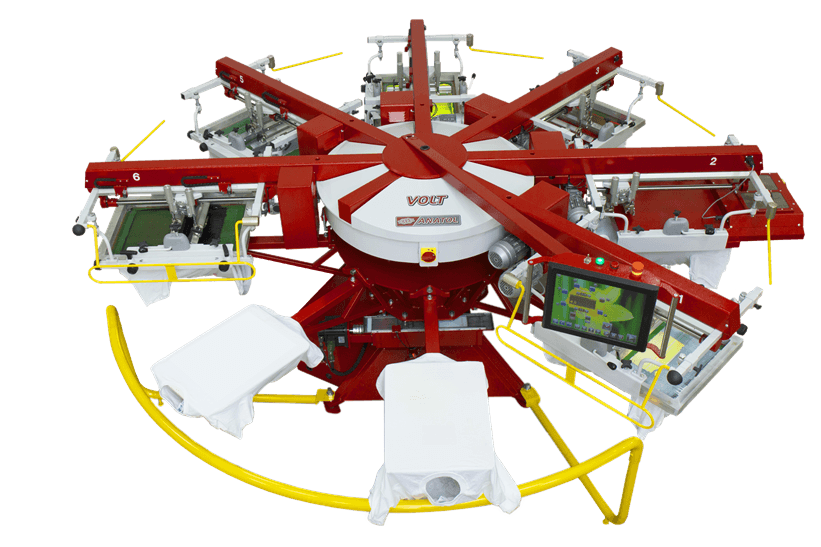
Think it might be time for your screen printing shop to upgrade from a manual press to an automatic? An automatic press can undoubtedly help you turn around bigger and more complex jobs in less time, as well as improve the overall consistency of your prints. Adding your first automatic press to your equipment arsenal can take your shop to the next level of productivity and profitability. Still, it’s essential to do your homework and thoroughly prepare your shop before making a purchase.
An automatic press is a significant investment. However, doing your due diligence helps ensure you get the suitable machine for your business’s current and future needs and that the transition to automation goes as smoothly as possible. Here are some tips to get you started.
Decide on a configuration for your screen printing needs
Automatic presses are available in a tremendous variety of sizes and configurations, which can be overwhelming for a first-time buyer. Your manual press may have limited your capabilities to small runs of simple one- or two-color designs. An automatic opens up a world of new possibilities. When choosing an automatic press, don’t only consider the type of work you’re doing now, but look to the future. How do you see your business evolving in the next few years? Are you regularly passing up larger or more complex orders because of the limitations of your manual equipment? When deciding on a configuration, ask yourself the following questions:
- What size print area do I need?
- How many colors do I need to be able to print?
- What size press can I fit in my shop?
Answering these questions helps narrow down your choices to the automatic presses that meet your absolute necessities. From there, you can start to compare their unique features and weigh the pros and cons. For example, how is the press powered? A pneumatic (air-powered) press might have a smaller upfront cost and make sense if your shop already has an adequate air compressor and chiller. An all-electric machine can save you money in the long run with better reliability and efficiency without requiring a costly compressed air system for operation.
Prepare your budget
Your available budget plays a decisive role in determining how much press you’re able to purchase. Automatic presses can run anywhere from $20,000-$200,000, depending on the configuration. In general, you should buy as much as you can reasonably afford; it’s more cost-effective to buy an automatic press that your business will grow into than a press you will quickly outgrow and need to replace. If you ask your fellow screen printers, very few will complain about having purchased an automatic press that was too big. In fact, it’s typically the opposite.
You also have to factor in the cost of freight, installation, training, and any upgrades you’ll need to make to your shop or other equipment. Many equipment sellers can provide third-party finance options for qualifying customers. Financing can make an automatic press purchase more accessible, but keep an eye on the overall cost and make sure that your payment plan makes sense for your business in the long run.
Consider your timeframe
Getting an automatic press up and running in your shop will not happen overnight. Even if your chosen supplier has your desired press in stock, the press must go through a thorough quality control inspection before it ships out to you. A factory technician typically has to perform the installation and training, which can be a 2-3-day process. If your press is built to order by the manufacturer, the lead time can increase quite a bit, especially as the global supply and logistics chain continues to strain under the effects of COVID.
With these challenges in mind, be prepared to wait three months or more before you’re printing the first shirts on your new automatic press. Be patient and use the lead time to prepare your shop for the new press’s arrival. Make sure you have adequate space available, your shop meets all applicable codes and regulations for your locality, your electrical supply is in order, and your ancillary equipment (particularly your conveyor dryer) is a good fit for the demands of the automatic press. It will be worth the wait!