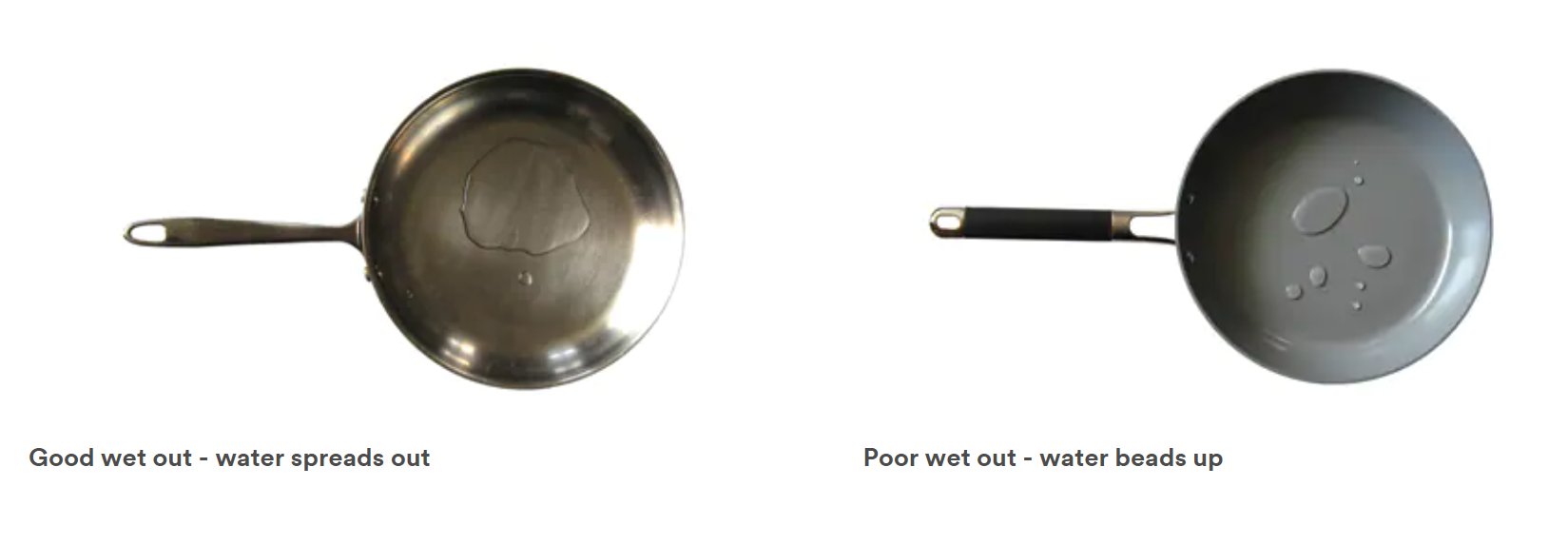
One of the early challenges of films is not knowing how well they will adhere to a surface. For example, what type of paint has been used on a wall? Is it a low-VOC paint with a greasy texture or paint that has been chalked over? PSPs can quickly and easily ensure the best outcome for their client by using an adhesion test kit to determine a film’s adhesion to many substrates and confirm the best material for the surface.
Adhesion test kits determine a substrate’s surface energy. Surface energy ranges from high to low. To illustrate the concept of surface energy, think of water on the unwaxed hood of a car. The unwaxed hood has high surface energy and water on the hood flows into puddles. In comparison, a waxed hood has low surface energy, and the water beads up rather than flows. Similar to water, adhesive on a high surface energy surface flows and “wets out” the surface. “Wetting out” is required to form a strong bond.
The following illustration of surface rankings gives you an idea of relative surface energy.
As a rule of thumb, the higher the surface energy, the greater the strength of adhesion. Specially formulated adhesives are available for low surface energy surfaces. Regardless of surface energy, most substrates must be:
- Clean: All substrates must be considered contaminated and must be cleaned prior to application of film or sheeting, with the last cleaning step being done immediately before application. Keep in mind that a freshly cleaned or painted substrate can quickly collect dust. Test cleaners in an inconspicuous area before using, as some may dull the surface or leave contaminants on it. Cleaners with a low solvent content may not remove the type of contaminants you have. For wall applications, be sure to clean the edges under the ceiling and all corners — these areas are easily overlooked.
- Dry: Any moisture trapped beneath the graphic can cause the graphic to fail prematurely. Moisture prevents the adhesive from adhering correctly, can cause bubbles, and can freeze in cold environments. Moisture results from inadequate drying after cleaning, failure to pre-dry some substrates (like polycarbonate sheeting), condensation at low temperatures, and high humidity environments.
- Relatively non-porous: Porous materials absorb moisture that affects the ability of the film or sheeting to adhere to the surface.
- Smooth: It is more difficult for the adhesive to make good contact with textured surfaces rougher than 150 grit sandpaper.