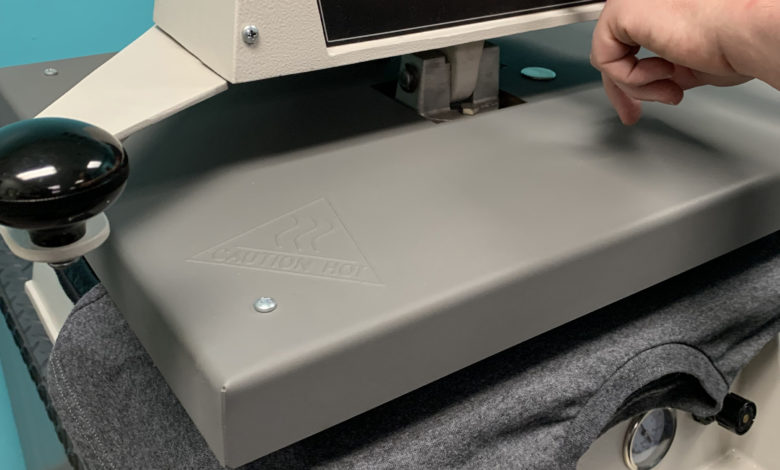
Finding the perfect decorating solution for your garments, flawless production runs, and happy return customers — It’s what you want! But your production is stuck on pause.
Be proactive rather than reactive when pairing your garments with the proper heat transfers. Do your homework and test before production starts. Being proactive when pairing garments with heat transfers provides superior product results compared to having to react to a situation gone wrong. Proactive steps always result in happy customers with repeat business.
Growing up, my father always stressed the fact of measuring twice and cutting once. This has been one of the most valuable lessons I have ever learned to this day. I live by this mantra on the job, and I even found myself using this theory in everyday life. The more information you have and the more you prepare for projects, the better the outcome.
“Practice makes perfect.”
A few months ago, we had a new customer who seemed to want to “wing it.” They asked for a particular heat transfer they had seen at a trade show to complement the garment they planned on using for their program; a transfer with a soft hand and excellent stretch. We sent them a sample pack of the transfer product they wanted to test on their fabric, but we informed them that we would not recommend using that product due to the fabric content. The transfer was not the best-suited product for their particular substrate.
The customer informed us that they had tested the transfer on the material and were satisfied with the results. They placed an order, and once the customer received their transfers and started production, they quickly realized that the adhesion was not what they expected. As quickly as they noticed the problem, they reached out to us. We explained the transfer was not the product we had recommended using for this fabric and discussed the best option for them.
We sent them a transfer sample pack of the product we did recommend, alongside a shortlist of tests to perform to ensure this product succeeds where the other did not. They applied the transfers and performed the tests we recommended. The results were good, the customer was satisfied, and they learned a valuable lesson in the process.
There are many factors to consider when creating and planning the production of decorated apparel. Here are three important areas you should look into when preparing an order for your customers.
Garment knowledge
Always know the content of the material you will be using. This is one of the most important factors of all. Remember, the garment always comes first. The substrate you apply the heat transfer to matters.
There is a range of materials used when it comes to the makeup of a garment. Some of these fabrics are widely used across many different garment markets. For instance, if you are applying heat transfers for team sports, you will most likely find the main content of the material to be polyester. Dye migration is an essential factor to consider. When applying to polyester, always test for dye migration.
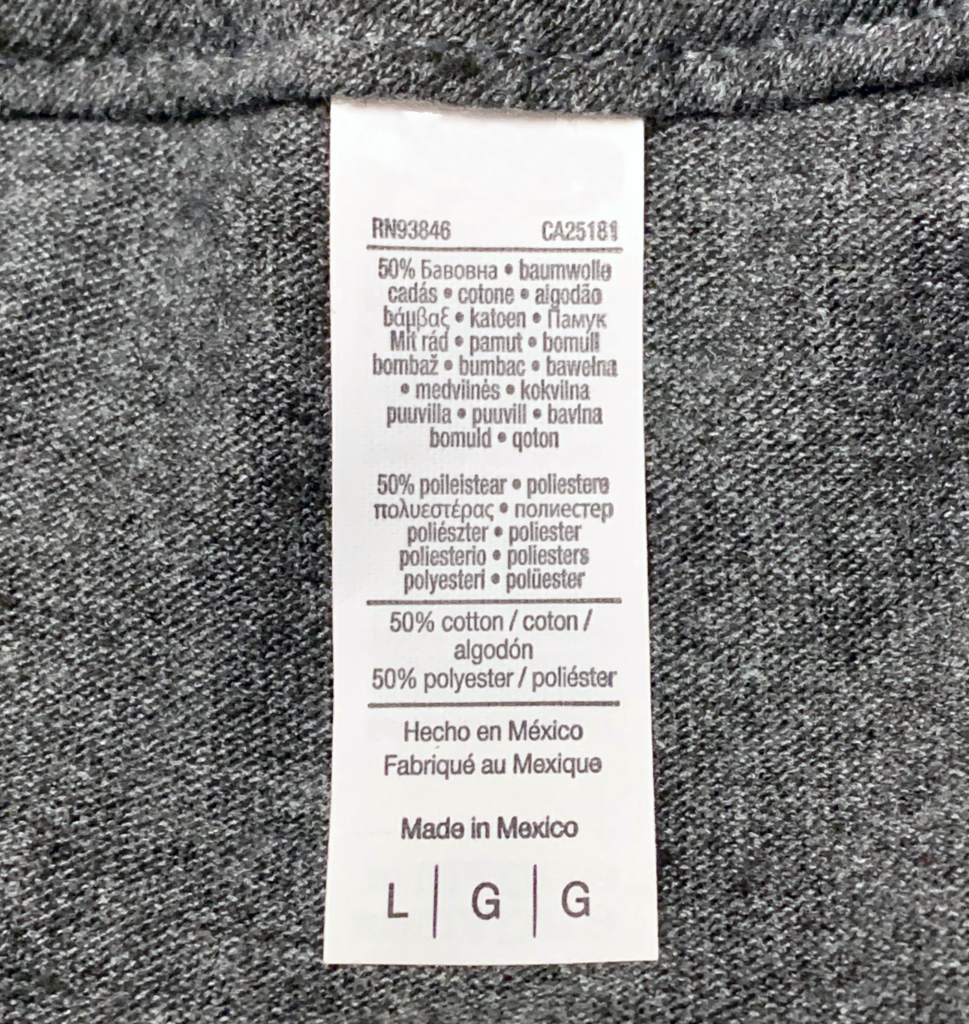
The next question you should ask yourself is: How does the transfer adhere to the garment? Wash testing is usually done to ensure that there is proper adhesion. Next, does this fabric have stretch or not? You don’t want to fuse a non-stretchable heat transfer on a stretchable garment. The transfer will most likely crack or feel like a sheet of plastic when worn.
Think about the market you will sell to. Think about the end-user of the garment you are decorating for and ask yourself, what will they be doing in this garment, and will this transfer hold up to their expectations?
In my opinion, it all comes down to four factors: Functionality, appearance, hand feel, and durability. If you are hitting all four of these points, you are headed in the right direction.
Design & art preparations
The size of the graphic to be applied to the substrate is very important. Measure the available image area on your garment. You don’t want to prepare your heat transfers, start production, and find out that the image is too big or doesn’t look right.
Graphic placement or location on a garment is critical when planning on what size to make your image. Full front, center chest, left chest, full back, and yoke are just a few examples of locations on a garment. It’s worth taking the time to get the graphic to the best-suited size for the garment and the location of the image.
Sometimes you might have small line weight text or thin lines in a graphic. Make sure that your artwork meets the minimum line weight requirements of the product you want to use. Be mindful of this factor because the smaller the line weight, the less durable the transfer will be in the wash.
Application & production processes
Testing your application process before starting your production ensures you have the best heat press settings suited for the garment. The first thing is to test to see how heat-sensitive your garment is. Check with the heat transfer manufacturer on which of their products they recommend to be used for your particular fabric. Transfer manufacturers usually provide suggested fabrics for the heat transfer products they sell.
Be cautious when testing the adhesion of a heat transfer when applying at low or lower temperatures than recommended. You can apply the transfer, and it might look great but once put in the wash, the graphic could start peeling off or start to crack if the adhesive or inks are not fused correctly.
Once you have dialed in the heat press settings and tested the transfer/garment, start thinking about production and what you can do to make this process consistent and as easy as possible. We call these production protocols.
Heat transfers call for the carrier to be peeled cold, warm, or hot. For high-volume runs, hot-peel transfers are ideal. Cold-peel heat transfers also work great for large runs, but you want to adjust your production protocols to create the quickest and most consistent production process.
What it all boils down to is the better you know your garments and the capabilities of the heat transfers you are using, the more successful the final result will be.
Don’t forget, testing your garments, heat transfers, and application processes can save you a lot of time, heartache, and money!