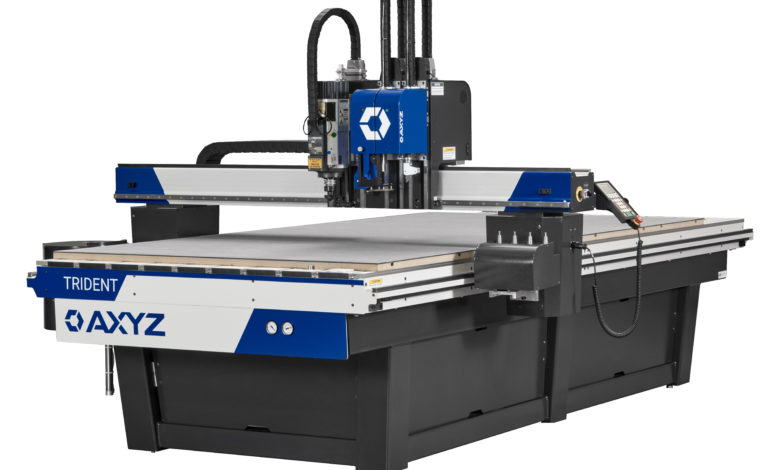
You may be wondering what you can do as a shop to prepare for the arrival of a CNC router. Here are some commonly asked questions answered.
What does a shop need to do to its physical location to prepare for a CNC router’s arrival?
Shop management will need the machine’s footprint drawing and use that to plan out where the physical machine will sit, how material and product will be loaded and unloaded, and where air and electrical power will be relocated.
How can the shop owner and employees prepare for the addition of a CNC machine?
The addition of a CNC router requires shops to pick a lead CNC operator. Find one that offers training and technical support and goes over the basics of a CNC router and shows the lead operator(s) the machine’s day-to-day operational requirements. We recommend preparing some real projects to be a part of the training with any technical specialist—this aids in integrating the new cutting technology.
How can a shop determine whether a CNC is even a good purchase?
CNC technology varies in its usage and application. A shop’s needs will depend on projected future growth and expansion. For example, a shop that manufactures aluminum composite panels (ACP) will look at leaving the current process of using a vertical panel saw in favor of using a CNC router that can cut, vgroove, and produce designs that are much more complex. Now, if that same shop is considering processing sheet metal and would like to insource it, the choice of CNC will expand, and the customer will look at CNC lasers, waterjets, or plasma machines.
How will a CNC machine impact an existing printing operation?
Using CNC routers in a production environment where other parts or processes require other equipment will require companies to review things like floor space, dust, debris, and software. Adding another piece of equipment involves consideration of workflow. CNC routers often leave some level of dust and debris on the worktable, and it is often the case that the dust can linger around the workshop.
For example, UV printers require a clean and dust-free environment, so placing the two pieces of equipment next to each other is not always recommended. Now, a robust dust collection system and adequate maintenance and cleaning operations—like prohibiting the use of compressed air by the operator to clean the machine or parts—will reduce the amount of dust.
Are there any additional challenges this equipment presents? If so, what are they?
Technical expertise: The learning curve for first-time CNC users can be challenging if you are not prepared. The good news is that printing software and cutting software work well together. Plus, the application teams and manufacturers you work with should have a wealth of knowledge and expertise available to you.
When using a CNC router, the consideration of speeds and feeds, tooling, coolant, hold down and cutting strategy all form the basics of operation knowledge, which is where the importance of technical support and specialists come into play.
For more on how to prep your shop for a CNC router, check out this article.