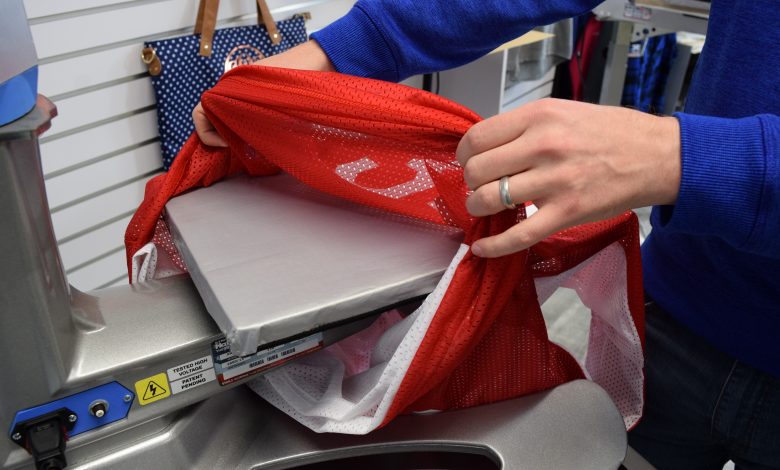
The most important instruction for heat printing reversible jerseys is getting to a single layer of fabric. Keep in mind that most jerseys are mesh, and simply laying them on top of your heat press for application will result in the sides sticking together. Also, merely splitting the jersey at the body will not be enough as there will still be two layers of mesh fabric per side, causing issues with printing and wear. A decorator must get the jersey down to a single layer, but don’t worry, almost all jerseys can do this.
While a print pad/large mousepad will do the trick, a heat press with a cantilever design is the most efficient option to split and load the jersey.
Consider that the 16″ X 20″ or 15″ X 15″ platen on most presses will probably be too wide for the upper back print location on a basketball jersey, causing the garment to get caught when trying to place a personalized player name. Therefore, many experienced heat printers prefer to utilize an 11″ X 15” lower platen and restrict the width of a player’s name to 10.75″ or less for this application. Heat presses often have interchangeable platens, which make swapping to an 11″ X 15″ platen easy.
With the jersey loaded appropriately, its time to discuss printing. Screen-printed transfer numbers often come in individual packs or kits with one digit per sheet. It’s crucial to select a transfer ink formula that works well on polyester. Although most ink formulas will work for polyester, there is not a guarantee that a particular transfer won’t have bleed through—dye block numbers or even numbers that apply at a lower temperature help to address this issue.
When it comes to placement, if your transfer supplier prints the numbers on a consistently sized sheet, it is easy to position a single or double-digit number for application. Simply align the two numbers together on the press and heat apply. Be sure to consider the pre-spaced name location for the back of the jersey if this is needed. Many decorators select a heat transfer film to match their numbers and cut them on a vinyl cutter. However, it can be difficult to match this correctly, so transfer companies often offer pre-spaced names you can order from a rostered list of players. This option keeps everything matching and makes for a very seamless experience when applying the jerseys.
Many screen-printed transfer products apply in as little as 4–15 seconds (depending on the ink formula) and are almost always a single-step application. Depending on your speed of placing the components, this should allow you to print both the front and back of each side of the jersey (four locations total) in two minutes or less. If you find that placement on the jerseys is slowing down production, consider a heat press with an integrated laser alignment system to speed up the process or add a stand-alone laser system to your current setup.
While this may seem like many considerations, it’s quite easy when you have the right tools for the job. Team decorators that spend the time to figure this out can enjoy a business segment that many printers turn away because of the headaches associated with not doing it correctly.